The Horticultural Physiology Lab has done much research on drought stress and plant responses to different irrigation regimes. To do this research the way we wanted to, we had to develop our own irrigation control systems, giving us the level of control over irrigation that we felt was necessary.
The principle behind these irrigation control systems is simple: we use soil moisture sensors to measure the volumetric water content of the soil or substrate and if the water content is below a particular threshold, we briefly open an irrigation valve to irrigate that particular plot. The irrigation controllers we have built have evolved over time. We initially used Campbell Scientific CR10(X) dataloggers with Decagon ECH 2 O-10 soil moisture sensors. More recently we have used Campbell Scientific CR1000 dataloggers with Decagon EC-5, 10HS, or GS-3 sensors. We also built low-cost irrigation controllers using Arduino (Uno and Mega) microcontrollers using 10HS sensors.
This page is meant to help you understand the evolution of our work and the pros and cons of different systems. Some of the information here may help you build your own soil moisture sensor-controlled irrigation system.
16 plots using a CR10X datalogger and ECH2O-10 sensors
We started with a CR10X datalogger and ECH 2 O-10 soil moisture sensors. This system was built by former PhD student Krishna Nemali. Sixteen soil moisture sensors are connected to an AM25T multiplexer. The multiplexer is needed, because the datalogger does not have enough ports to allow all sensors to be connected to the datalogger. Using the multiplexer, the datalogger can get readings from all 16 sensors, with each sensor in a separate plot. The datalogger compares the measured volumetric water content to an irrigation threshold for that particular plot. If the water content is below that threshold, the datalogger open an irrigation valve for a brief, user-specified time, using a Campbell Scientific SDM-CD16AC relay driver.
Krishna Nemali presented a poster describing the system at the 2005 meeting of the American Society for Horticultural Science and won 1 st place in the graduate student poster competition. We also published a paper in Scientia Horticulturae describing the system:
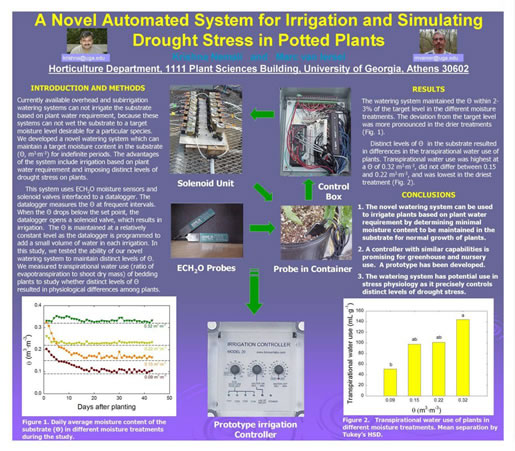
The datalogger program that ran the system is available from this web page in both PDF and CSI format (the actual program is written in CSI format, using Campbell Scientific’s EDLOG software).
32 plots using a CR10X datalogger and EC-5 or 10HS sensors
Although V1.0 of our irrigation controller worked well, it had two major drawbacks:
- We wanted to control more than 16 plots
- The ECH2O-10 sensors are capacitance sensors operating at relatively low frequency, making them sensitive to the electrical conductivity of the soil or substrate. The sensor also turned out to be temperature sensitive.
We published our evaluation of these sensors in 2007:
We addressed these issues by:
- replacing the AM25T multiplexer with an AM16/32 multiplexer, which can measure more sensors
- adding another SDM-CD16AC relay controller, which allowed us to control an additional 16 plots
- Replacing the ECH2O-10 sensors with EC-5 or 10HS sensors (depending on the study). EC-5 or 10HS sensors measure capacitance at a higher frequency, making them less sensitive to electrical conductivity. These sensors are also less sensitive to temperature.
These changes did not change the fundamental performance of the system, but provided more accurate substrate water content readings and allowed for more treatments and/or replications. At times, we also used two sensors per plot and averaged the readings from those to determine when the plants needed to be irrigated.
An example program, with two EC-5 sensors in each of the 32 plots can be downloaded here: 32 PLOT IRRIGATION CONTROL, EXAMPLE.CSI
Controlling subirrigation
Our initial work with soil moisture-based irrigation control focused on drip irrigation systems, which allowed us precise control over substrate water content. We have since expanded our work to subirrigation as well by Rhuanito Soranz Ferrarezi, a visiting PhD student from Brazil. For subirrigation applications, soil moisture sensors allow us to determine how dry a substrate gets before a subirrigation event is triggered. Since we cannot control how much water is absorbed by the substrate during subirrigation, the substrate water content typically rises quickly during irrigation. So this approach does not provide the same level of control of substrate water content, but it is an effective way to control irrigation and it can be used to alter plant morphological responses. For an example of our work on irrigation control in subirrigation, please see:
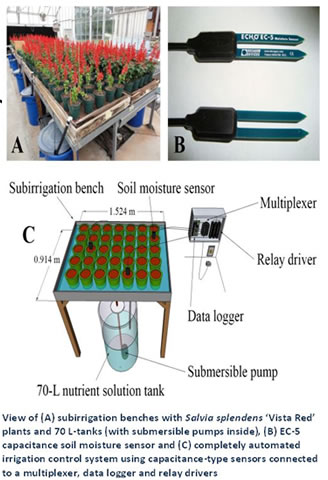
Ferrarezi, R.S., Marc W. van Iersel and R. Testezlaf. 2014. Subirrigation automated by capacitance sensors for salvia production. Horticultura Brasileira 32:314-320. https://dx.doi.org/10.1590/S0102-05362014000300013.
Low-cost irrigation controllers: Arduino
Initially, we used Campbell Scientific dataloggers to build our irrigation controllers. Although this works fine, Campbell Scientific dataloggers are fairly expensive. The advent of low-cost, open-source microcontrollers provides exciting new possibilities for building many kinds of automated systems, including irrigation controllers. We have chosen to work with Arduino microcontrollers, because they are low-cost and there is a tremendous amount of information and examples available on-line. Post-doc Rhuanito Soranz Ferrarezi has done much of the work in this area.
The basic principle is the same as that of our earlier Campbell Scientific datalogger-based controllers. We have used two microcontrollers, the Arduino Uno and Mega. Both microcontrollers are fully capable of irrigation control, but the Arduino Mega can measure a larger number of sensors and can control more valves (up to 32 using a multiplexer). As with the Campbell Scientific dataloggers, a relay control board is needed to allow the Arduino Uno or Mega to open and close valves.
Neither the Arduino Uno nor Mega is capable of storing data, which is obviously a problem for research applications. To build a system capable of data storage, an SD shield is needed. These shields can simply be plugged on top of an Arduino board and they add the capability of storing data on an SD card. Our paper describing Arduino-based irrigation system is available here:HortTechnology 25(1) 110-118 2015
If you are interested in how to do this, you can download our pictorial guides and software (or sketches as they are commonly called).
Building a 4-plot irrigation controller using an Arduino Uno.pdf (PDF file)
Building a 14-plot irrigation controller using an Arduino Mega.pdf (PDF file)
Arduino Uno irrigation control program in text or ino (Arduino) program file.
Arduino Mega irrigation control program in ino (Arduino) program file.
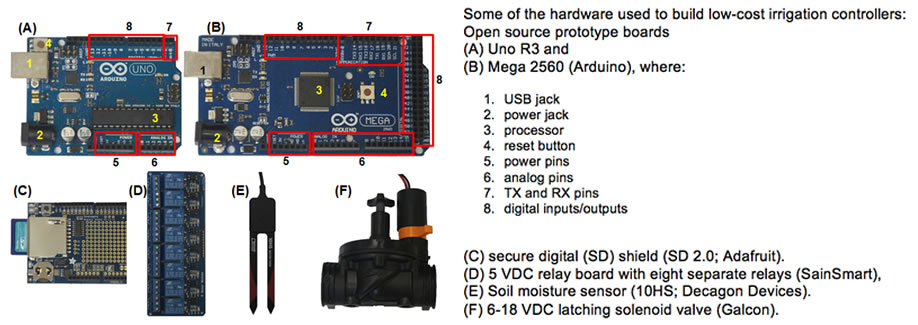
Irrigation and fertigation control
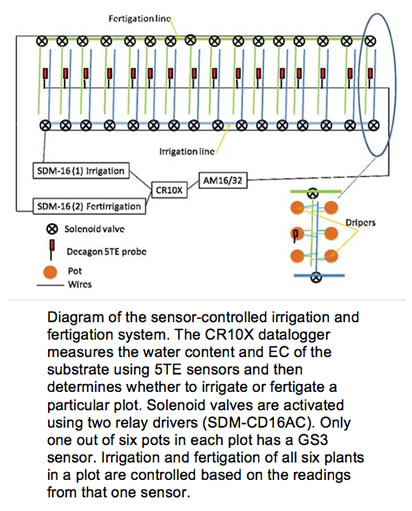
Although controlling irrigation has been a great tool for our work, we have not been satisfied: we also want to be able to automatically control fertilization. In greenhouses, fertilizer is commonly applied dissolved in the irrigation water: fertigation. Since dissolved salts increase the electrical conductivity (EC) of soils, substrates or solution, the greenhouse industry commonly uses EC as a proxy for substrate fertilizer levels. Using sensors that can measure both substrate water content and EC in principle allows us to irrigate when plants have adequate fertilizer but need water or fertigate when plants need both water and fertilizer.
Initial work on this was done by Julián Miralles Crespo, a visiting PhD student from Spain. We used a Campbell Scientific CR10X data logger to measure Decagon’s 5TE sensors, which can measure both bulk EC and substrate water content. These data were then used to calculate pore water EC (using the Hilhorst (2000) approach). Our results showed that controlling substrate volumetric water content is easier than controlling the EC of the pore water in the substrate. However, the results also suggested that automated control of substrate water content and pore water EC is possible, but that better EC sensors are needed. Julián presented our findings at a conference in Spain. This link will get you to our paper.
One problem with the 5TE sensors is that the electrodes that measure EC are small. That is problematic when using these sensors in highly porous soilless substrates, because there may not be good contact between the electrodes and the substrate. Decagon has since released GS-3 sensors, which were designed specifically for highly porous substrates. We are now testing those sensors, connected to a CR1000 datalogger, for automated irrigation and fertigation control.
Wireless sensor networks – Improving Irrigation with Sensor Networks: Implementation and Impact
From 2009 to 2014, we participated in a USDA-AFRI-SCRI project (#2009-51181-05768) with as the main goal to provide growers with the ability to precisely monitor and control applications of water and nutrients to plants in these production settings, based upon daily plant requirements. Team members in this project developed wireless sensor networks, including hardware and software (especially Decagon Devices and Carnegie Mellon University’s Robotics Institute). Other team members worked on on-farm implementation and use, irrigation modeling, plant responses, and economic and societal impact. For more information on this project, please go to www.smart-farms.net or www.smart-farms.org (the knowledge center with learning modules for users).
For detailed descriptions about what we did during the first four years of the project, please read our series of papers in the December 2013 issue of HortTechnology
Using Normalized Difference Vegetation Index (NDVI) as a Proxy for Plant Size in Water Use Models to Facilitate Precision Irrigation
Shuyang Zhen and Marc W. van Iersel
VIDEO COMING SOON
Root Disease Incidence and Severity in Nursery Crops with Soil Moisture Sensor-based Automated Irrigation
William Wheeler, Matthew Chappell, Paul A. Thomas, Marc W. van Iersel and Jean Williams-Woodward
VIDEO COMING SOON
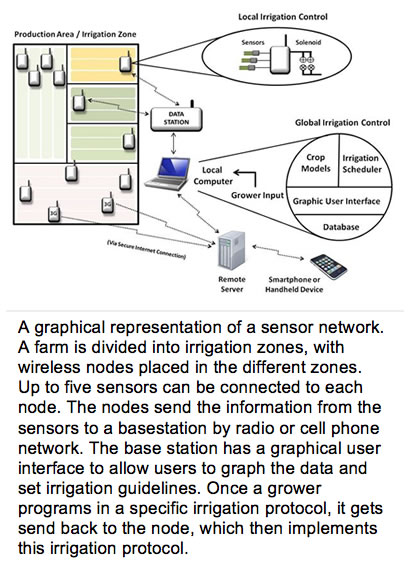
Note: much of our work on irrigation control has been with a great team of collaborators, both within our lab and from around the world. In the Horticultural Physiology lab, the following former and current students and visiting scientists have worked on this: Krishna Nemali, Jongyun Kim, Lucas O’Meara, Alem Peter, Mandy Bayer, Alex Litvin, and Shuyang Zhen. Other collaborators from the University of Georgia include Drs. Matthew Chappell and Paul Thomas.
Other collaborators include: Dr. Stephanie Burnett at the University of Maine, Drs. John Lea Cox, Andrew Ristvey, John Majsztrik, Erik Lichtenberg, and Dennis King at the University of Maryland, Taryn Bauerle at Cornell University, Bill Bauerle at Colorado State University, David Kohanbash and George Kantor at Carnegie Mellon University, Lauren Crawford, Colin Campbell, Todd Martin, Chris Lund, and others at Decagon Devices.